Solar energy is becoming an increasingly popular choice for homeowners and businesses looking to reduce their carbon footprint and save on electricity bills. Some of the common questions that arise when considering a solar installation are, “How many panels do I need for a 10KW solar system?” and how much does a 10KW solar system cost?
In this article, we will explore the factors that determine the number of panels required for a 10KW solar system and provide some insights into the planning process.
…
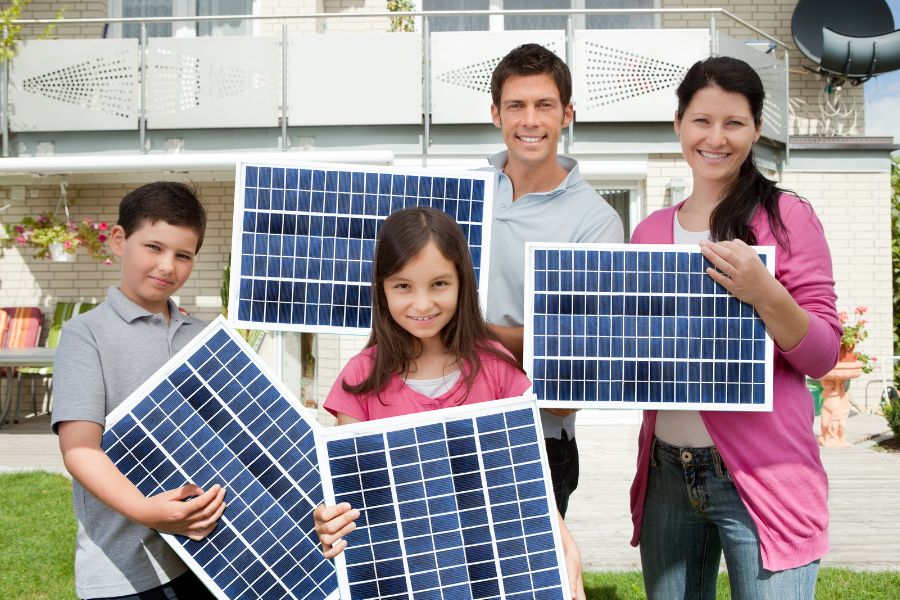